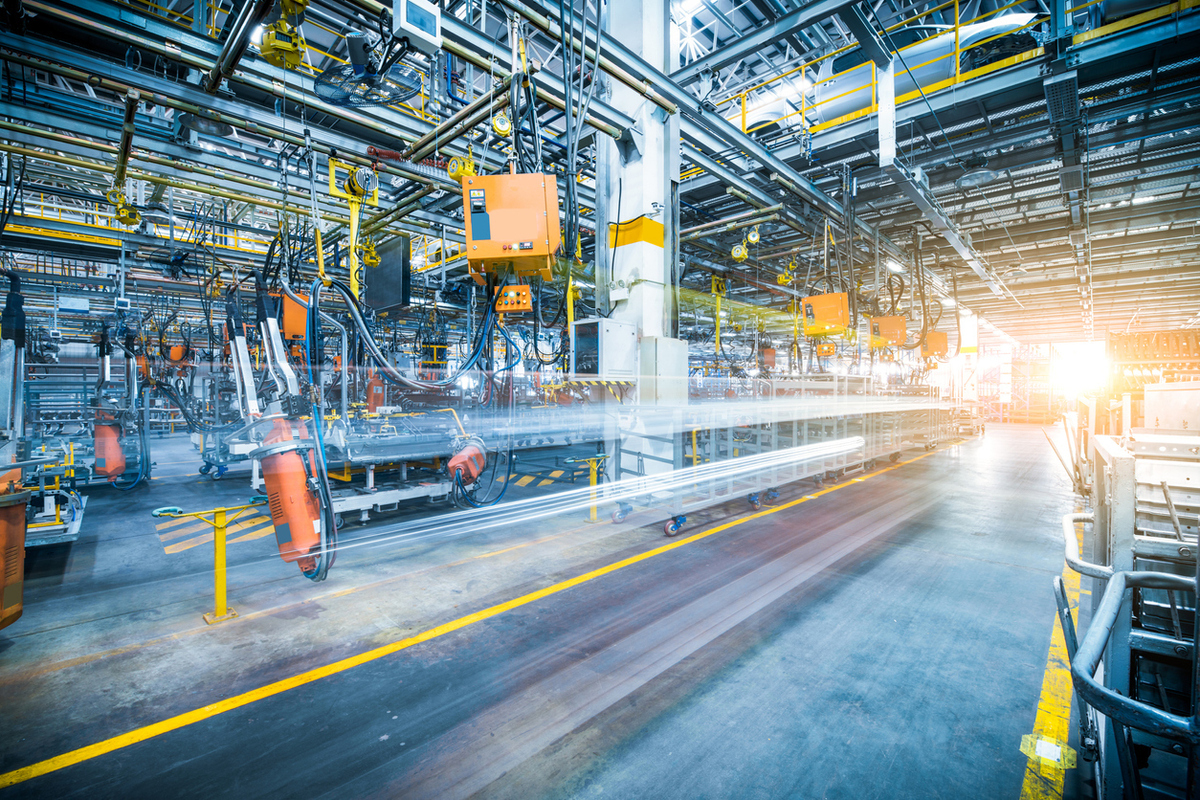
By Christian Reichenbach and Matthias Roese | 20 JULY 2021
Collected at: https://www.cio.com/article/3625523/from-automated-to-autonomous-manufacturing-industry-digital-transformation.html?utm_source=Adestra&utm_medium=email&utm_content=Title%3A%20From%20Automated%20to%20Autonomous%20%E2%80%93%20Manufacturing%20Industry%20Digital%20Transformation%20&utm_campaign=CIO%20Daily%20News&utm_term=CIO%20UK%20Daily&utm_date=20210805140743&huid=5e0c1b34-7735-4637-b4ec-d75bc72cdc0e
The manufacturing industry is one of the leading sectors starting or speeding up digital transformation. Particularly hard hit by supply chain issues, the sector wants to ensure resilience to business disruption and not be caught again by events with global consequences. To date, however, they have met with varying success. Many of the transformation pilot projects do not land in production, the core of business, and fail to contribute to improved business outcomes. If organizations are failing to scale proof-of-concept to production environments, what is needed to successfully deploy digital models?
Hewlett Packard Enterprise (HPE) Digital Advisors recognized the value of a framework that helps enterprises visualize what it takes, as well as capture all the moving parts to ensure alignment and prioritization. They developed the Digital Journey Map, a method which helps companies structure their transformational goals and succeed in achieving them.
Digitalization offers countless value to manufacturing companies. It can help transform operational and product processes fundamentally as well as make work more efficient, secure, and less stressful. Products can become more attractive and valuable through embedding them into a digital ecosystem. Instead of monolithic market offerings, companies can also offer them in a consumption-based, as-a-service models. Stabilized revenue streams, alternate markets, and strong customer loyalty are just a few of the positive outcomes. In addition, digitalization provides a better understanding of customer product usage, in turn feeding improved research and development and creating a virtuous circle.
Why do digitalization projects fail then?
Even 10 years after the invention of Industry 4.0 we see digitalization projects stuck in pilot phase and transfer to production not being successful. This was the case prior to the onset of the pressures of the global pandemic, but as we start to enter a phase of consolidation it’s exacerbated. Almost 50% of enterprises admit they’re not meeting the digital transformation speed management expects, compounded by lacking the wherewithal to do so.¹
Here are the main reasons:
- Process optimization instead of business optimization: Manufacturers still use technology predominantly to optimize existing business processes instead of transforming them. The real opportunities of digitalization are missed and their potential untapped.
- Over-focus on technology: Digitalization initiatives often start with great enthusiasm for a new, just-arrived, popular technology like machine learning, big data, or IoT. No one really checks if and how the implementation will bring value for the strategic and operational targets of the company. Only at the time of transferring from Proof of Concept (PoC) to production do they realize that the business advantage is minimal rationalized to the effort made, that important data or interfaces are missing, or that the model just does not scale for real production.
- Too many silos: Many PoCs are planned and implemented in one line of business without a view of the broader context. This results in limited benefits together with the risk that integration into the overall productive environment might fail due to resistance from other areas of the business. They have not been involved in the development, and therefore are not engaged.
- Insufficient data integration: We see data being collected and analysed only in individual areas such one specific production line. The value of data is very limited if it is not made available cross-business lines to be analysed in a broader view.
Making digital transformation for the manufacturing industry successful
One important success factor for digital transformation is the utilization of existing data, all information available, and most important, the collective knowhow of an agile, open, new digital world. Instead of optimizing one production step it is essential to recognize the overall context and realize the actual benefits of using available technology.
Digital Advisors show how this can work using the HPE Digital Journey Map. It is based on three essential capabilities of a digital organisation: digitalization at the Edge, a cloud-enabled IT supply chain, and a data infrastructure that can connect both. The framework consists of four “Journeys,” all of which are aimed at business goals captured within the framework of a digital strategy:
- Redefine Experiences: Digitalization changes the user experience at the edge but also changes the way of working, efficiency, and productivity of employees. Today we can increase work satisfaction by a better man-machine-collaboration or by freeing up employees from repetitive tasks. Video analytics solutions like those using the OpenVino toolkit (Open Visual Inference and Neural Network Optimization, Open Source/Intel®) enable automated and AI-based detection of anomalies and defects in manufacturing processes to relieve employees in quality assurance. Those systems can also be used to ensure workers’ safety. Intelligent cameras can autonomously watch the entrance of a danger area and identify any violation of protection regulations. If an employee tries to enter such a danger area without respective safety equipment the system will deny access.
- Gain Insight and Control: The more sensors deployed at the edge the more it is possible to capture and analyze production processes and usage patterns. With the help of the collected data, production can be controlled more efficiently and product development can be better aligned to real customer needs. One example is electro mobility battery production. It is a complex process because mechanical, chemical, and electrical requirements have to be merged and met. The length and complexity of the process chain creates a huge amount of data which has to be captured, saved, and analyzed.
- Accelerate Development: This journey concentrates on accelerating product-to-market through better collaboration between engineers, technology experts, and product managers. Exchanging information between the different teams and understanding the influence of all data at each step of the production process is a key challenge. A practical example can be found by looking at production and supply chains. Companies might use different software or different software releases for business tasks, managing their suppliers, or production control – all of which complicates data exchange. The problem can be solved by building a data-centric architecture which represents the basis for data flowing between supplier, partner, and customer in a data ecosystem. It decouples the data itself from the applications using that data by organizing them via a special data hub.
- Modernize and Move: Here we look at developing an optimized supply chain. Which technologies should be used? Do I implement cloud capabilities? Where do I need the expertise – in the data center or where data is created at the edge? These are the questions for this journey. Look at an example for a successful implementation of a Hybrid-IT-infrastructure with SAP S/4 HANA in a pay-per-use-Model, which meets two functions at the same time: an ERP-environment based on newest technology reflecting business processes, and a high-performance engineering platform satisfying the research and development department of a high-tech company.
The digital backbone
Each organization on this path needs a central data infrastructure. It is not enough to gather all data; it has to be correlated and analyzed cross-company. That said, the topic of trust is key to data strategy. Trust is more than IT security and data protection. It is a matter of which and how much data is collected, where and how long it will be saved, and data sovereignty. That also includes ethical aspects of data collection and analysis.
The path forward
To finally use the advantages of digitalization, companies must overcome the classical separation of information technology and operational technology, or IT and OT. It is not simply a matter of better cooperation from both; it is bringing the operating model to a new digital level, which integrates both domains. This also requires the cultural and organizational respective management of change, which must solve any resistance between departments touched and help merge teams. A data-centric architecture is also a significant part of the transformation that allows access to data cross applications. The end-state might well be that procurement of technology will be standardized and simplified without making any difference between IT and OT, facilitated by partnerships between IT and OT vendors.
Recognize external expertise is required
Moving from a technology-focus to consider the overall business model is key to improve and automate the new operating model. Companies implement technology not only to optimize processes, but to increase the value proposition of their products, develop new channels to their customers, revolutionize their production using new processes and technology, and embed their solutions into a bigger ecosystem and platform.
The HPE Digital Journey Map Webinar guides customers to success. It helps manufacturing companies better orchestrate their digital transformation, putting single initiatives and projects in a meaningful sequence, and at the same time helping them formulate clear goals and objectives for their digitalization strategy.
To find out more about Digital Next Advisory or engaging with an HPE Digital Advisor please contact us at digitaladvisors@hpe.com
¹The state of Digital Transformation Today.2020. Celerity.com